按牙型可分為三角形、梯形、矩形、鋸齒形和圓弧螺紋;
按螺紋旋向可分為左旋和右旋;
按螺旋線條數(shù)可分為單線和多線;
按螺紋母體形狀分為圓柱和圓錐等。
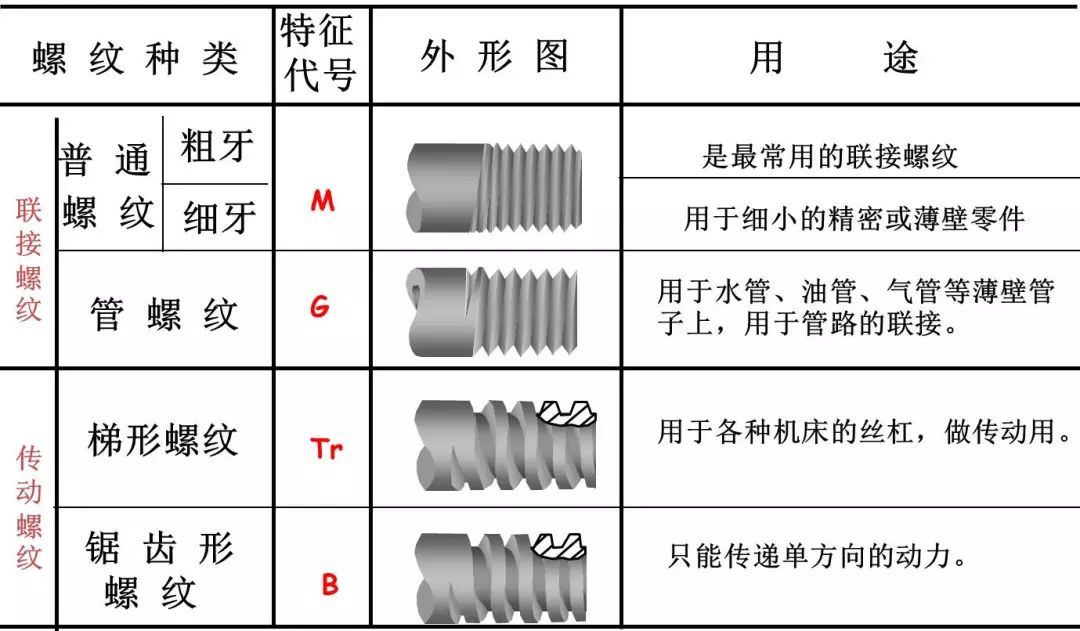
螺紋包括五個要素:牙型、公稱直徑、線數(shù)、螺距(或導程)、旋向。
1. 牙型
在通過螺紋軸線的剖面區(qū)域上,螺紋的輪廓形狀稱為牙型。有三角形、梯形、鋸齒形、圓弧和矩形等牙型。
螺紋的牙型比較:

螺紋有大徑(d、D)、中徑(d2、D2)、小徑(d1、D1),在表示螺紋時采用的是公稱直徑,公稱直徑是代表螺紋尺寸的直徑。
普通螺紋的公稱直徑就是大徑。

沿一條螺旋線形成的螺紋稱為單線螺紋,沿軸向等距分布的兩條或兩條以上的螺旋線形成的螺紋稱為多線螺紋。
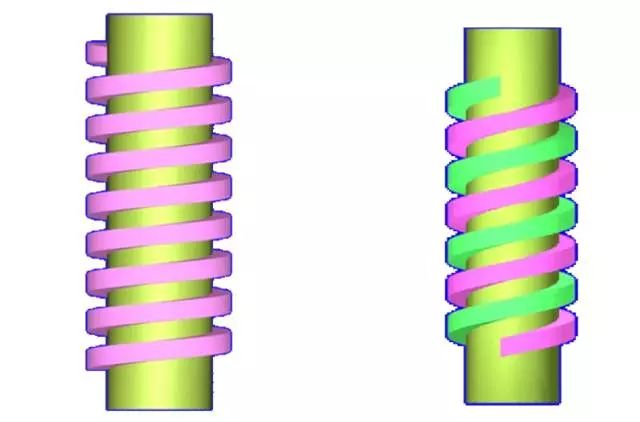
螺距(p)是相鄰兩牙在中徑線上對應兩點間的軸向距離。
導程(ph)是同一條螺旋線上的相鄰兩牙在中徑線上對應兩點間的軸向距離。
單線螺紋時,導程=螺距;多線螺紋時,導程=螺距×線數(shù)。
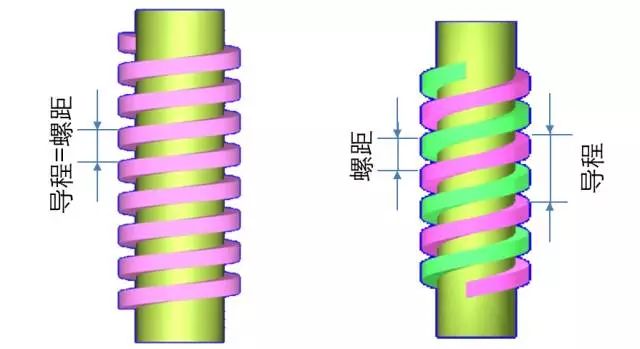
順時針旋轉時旋入的螺紋稱為右旋螺紋;
逆時針旋轉時旋入的螺紋稱為左旋螺紋。
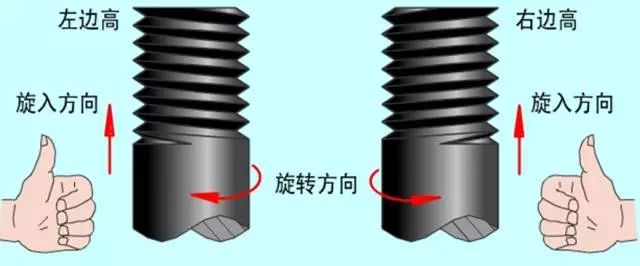
用螺紋加工工具加工各種內、外螺紋的方法。
一般指用成形刀具或磨具在工件上加工螺紋的方法,主要有車削、銑削、攻絲套絲磨削、研磨和旋風切削等。車削、銑削和磨削螺紋時,工件每轉一轉,機床的傳動鏈保證車刀、銑刀或砂輪沿工件軸向準確而均勻地移動一個導程。在攻絲或套絲時,刀具(絲錐或板牙)與工件作相對旋轉運動,并由先形成的螺紋溝槽引導著刀具(或工件)作軸向移動。
2螺紋車削
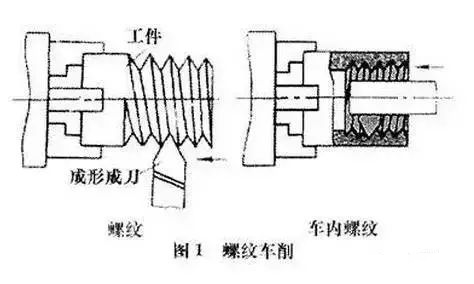
3螺紋銑削

4螺紋磨削
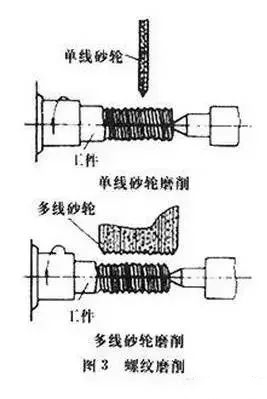
5螺紋研磨
用鑄鐵等較軟材料制成螺母型或螺桿型的螺紋研具,對工件上已加工的螺紋存在螺距誤差的部位進行正反向旋轉研磨,以提高螺距精度。淬硬的內螺紋通常也用研磨的方法消除變形,提高精度。
6攻絲和套絲
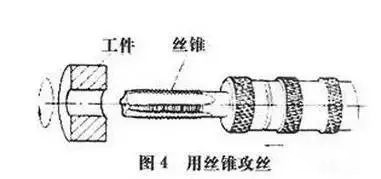
7螺紋滾壓
用成形滾壓模具使工件產生塑性變形以獲得螺紋的加工方法螺紋滾壓一般在滾絲機搓絲機或在附裝自動開合螺紋滾壓頭的自動車床上進行,適用于大批量生產標準緊固件和其他螺紋聯(lián)接件的外螺紋。滾壓螺紋的外徑一般不超過 25毫米,長度不大于100毫米,螺紋精度可達2級(GB197-63),所用坯件的直徑大致與被加工螺紋的中徑相等。滾壓一般不能加工內螺紋,但對材質較軟的工件可用無槽擠壓絲錐冷擠內螺紋(最大直徑可達30毫米左右),工作原理與攻絲類似。冷擠內螺紋時所需扭距約比攻絲大1倍,加工精度和表面質量比攻絲略高。
螺紋滾壓的優(yōu)點是:①表面粗糙度小于車削、銑削和磨削;②滾壓后的螺紋表面因冷作硬化而能提高強度和硬度;③材料利用率高;④生產率比切削加工成倍增長,且易于實現(xiàn)自動化;⑤滾壓模具壽命很長。但滾壓螺紋要求工件材料的硬度不超過HRC40;對毛坯尺寸精度要求較高;對滾壓模具的精度和硬度要求也高,制造模具比較困難;不適于滾壓牙形不對稱的螺紋。
按滾壓模具的不同,螺紋滾壓可分搓絲和滾絲兩類。
搓絲 兩塊帶螺紋牙形的搓絲板錯開 1/2螺距相對布置,靜板固定不動,動板作平行于靜板的往復直線運動。當工件送入兩板之間時,動板前進搓壓工件,使其表面塑性變形而成螺紋。
滾絲有徑向滾絲、切向滾絲和滾壓頭滾絲 3種。
①徑向滾絲:2個(或3個)帶螺紋牙形的滾絲輪安裝在互相平行的軸上,工件放在兩輪之間的支承上,兩輪同向等速旋轉,其中一輪還作徑向進給運動。工件在滾絲輪帶動下旋轉,表面受徑向擠壓形成螺紋。對某些精度要求不高的絲杠,也可采用類似的方法滾壓成形。
②切向滾絲:又稱行星式滾絲,滾壓工具由1個旋轉的中央滾絲輪和3塊固定的弧形絲板組成。滾絲時,工件可以連續(xù)送進,故生產率比搓絲和徑向滾絲高。
③滾絲頭滾絲:在自動車床上進行,一般用于加工工件上的短螺紋。滾壓頭中有3~4個均布于工件外周的滾絲輪。滾絲時,工件旋轉,滾壓頭軸向進給,將工件滾壓出螺紋。
螺紋加工常見問題及解決方法
